in this article, Amir is illustrating the use of tubular structural catalyst module to impove steam-methane-reforming process as Honeywell and ZoneFlow Reactor Technologies announced recently an agreement to commercialize such module.
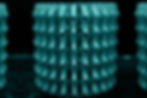
Hydrogen is typically produced by steam reforming of natural gas -often called steam methane reforming- in which methane is mixed with steam, then the mixed feed is heated inside reformer tubes -tubular reactors- and syngas is formed. Reformer tubes are packed with conventional pellet catalyst composed of nickel oxide. Usually, methane is used as burner fuel to heat reformer tubes. After leaving the reformer, syngas heat is utilized in steam generation or feed-effluent heat exchangers.
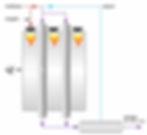
Process Development : Research Business
Zone Flow Reactor Technologies -headquarters in Connecticut, United States- is an emerging technical research company that specialize in methane steam reforming process development, with total capital investmenet of 15 million USD. Currently, the company operates a pilot plant in Louvain, Belgium to demonstrate the effectiveness of the new module. The structural catalyst module is based on “thermal sleeve” reforming reactor with higher thermal efficiency to reduce operational expenses. Thus, consuming less burner fuel and eliminating carbon emissions.
In this module, the firing chamber is the core tube, in which methane is used as burner fuel. However, flue gas is recirculated inside thermal sleeve (left) to heat the reforming process that takes place inside the reactor sleeve which is packed with structurtal catalyst (middle). Finally, produced syngas is recirculated inside another thermal sleeve (right) to maximize heat recovery. notice the cross-sectional thermal profile below.
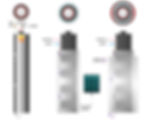
According to research paper titled “pressure drop and heat transfer of ZoneFlow™ structural catalytic reactors and reference pellets for steam methane reforming” by Florent Minette, Luis Calamote de Almeida, et al : structural catalyst improve heat transfer into tubular reactors by over 100% without increasing the pressure drop -flow indicator- across the reactor compared to conventional pellet catalysts, which is illustrated in the relative heat transfer versus relative pressure drop chart below.
